Understanding the fundamentals of LVL beams
When it comes to modern construction materials, Laminated Veneer Lumber (LVL) beams are among the most sought-after due to their exceptional strength and versatility. Understanding LVL beams is essential for builders looking to improve their project outcomes, whether it’s for residential or commercial applications.
What are LVL beams?
LVL beams are engineered wood products made by bonding together thin layers of wood veneer. These layers, often referred to as ‘plies,’ are glued under heat and pressure, resulting in a strong, stable beam that can support heavy loads. Unlike solid wood, which can warp and twist, and the LVL beams maintain their shape, making them a preferred choice in various construction applications. Their uniformity also allows for more predictable performance in structural applications.
Key characteristics of LVL beams
There are several noteworthy characteristics that make LVL beams a popular choice among builders:
- Strength: LVL beams have a high strength-to-weight ratio, making them capable of carrying heavy loads without excessive bulk.
- Stability: Their manufacturing process minimises the natural imperfections found in solid wood, resulting in a material that resists warping and splitting.
- Customisation: LVL beams can be manufactured in various sizes to suit specific structural requirements, which allows builders to work efficiently.
Moreover, LVL beams are not only strong but also environmentally friendly. The production process utilises fast-growing tree species, which can be harvested sustainably, thus reducing the pressure on slower-growing hardwoods. This makes LVL a more sustainable option for builders who are increasingly conscious of their environmental impact. Additionally, the ability to produce LVL beams in large quantities means that they can be readily available for projects, helping to keep construction timelines on track.
Another significant advantage of LVL beams is their compatibility with other building materials. They can be easily integrated with steel and concrete, providing architects and engineers with the flexibility to create innovative designs that utilise the strengths of each material. This adaptability not only enhances the aesthetic appeal of structures but also contributes to their overall functionality and durability. As a result, LVL beams are becoming an integral component in modern architectural designs, from residential homes to large commercial buildings.
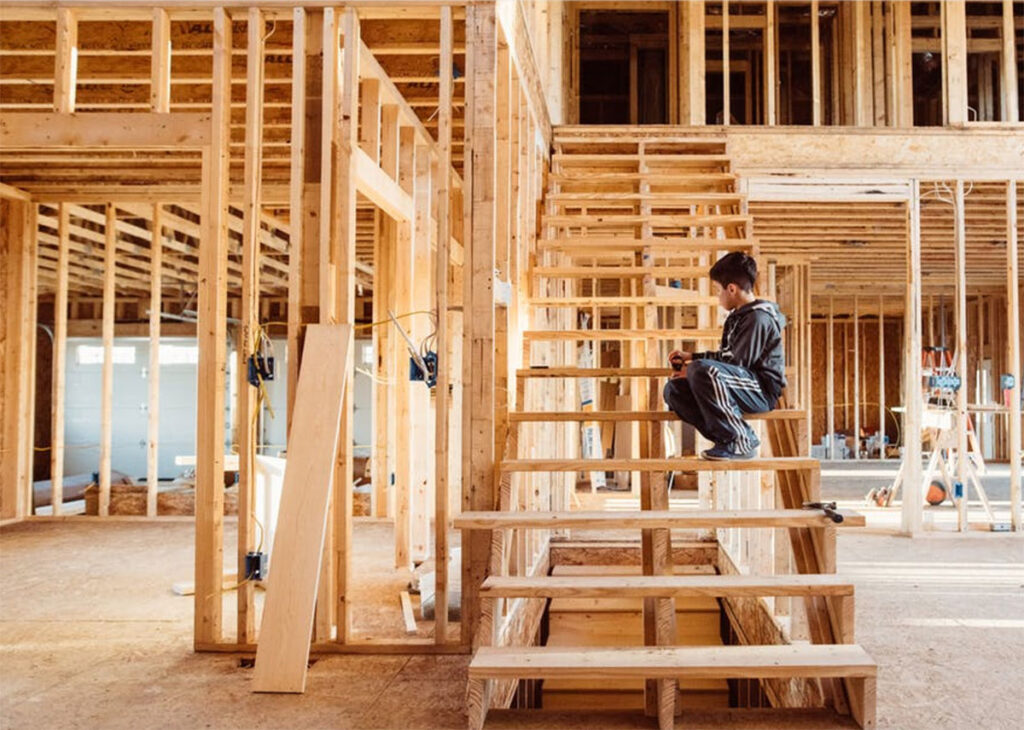
The manufacturing process of LVL beams
The journey of an LVL beam from raw material to a finished product is fascinating. It involves a systematic process designed to ensure strength and reliability.
Raw materials used in LVL beams
The primary raw materials used in the production of LVL beams are thin layers of wood veneer sourced from various trees, primarily softwoods. These veneers are usually around 3mm thick and are selected based on their quality and grain. In addition, a strong adhesive is applied to bond the layers together, ensuring the longevity and structural integrity of the product.
Click here to learn about lvl construction.
Steps in the production of LVL beams
The typical production process includes several crucial steps:
- Veneer Preparation: Logs are debarked and sliced into thin sheets of veneer.
- Drying: The veneers are then dried to a moisture content that is ideal for bonding.
- Gluing: Adhesive is applied to the veneers, and they are layered together.
- Pressing: The stacked veneers are subjected to heat and pressure in a hydraulic press.
- Curing: The beam is cured to allow the adhesive to set, ensuring strong bonds.
- Trimming: Finally, the beams are trimmed to the desired length, and quality checks are performed.
The benefits of using LVL beams in construction
Builders are increasingly recognising the myriad benefits that LVL beams bring to construction projects. These advantages extend far beyond simple strength and include various factors that positively impact overall project outcomes.
Strength and durability of LVL beams
The primary selling point of LVL beams is their exceptional strength and durability. They are specifically engineered to resist bending and deflection, making them ideal for use in load-bearing situations. Their ability to carry heavy loads means fewer beams are required, which can streamline construction time and reduce costs. Find more about deflection on https://knowledge.wharton.upenn.edu/article/deflection-good-business-tactic/
Versatility of LVL beams in building design
Another key benefit of LVL beams is their versatility in design. They can be used in a variety of structural applications, whether it’s floor joists, headers, or rafters. The array of potential sizes and shapes allows architects and builders to be more creative with their designs, enhancing both aesthetics and performance.
Common applications of LVL beams in building
LVL beams have found a place in numerous applications, showcasing their functionality and adaptability in various construction scenarios.
Use of LVL beams in residential construction
In residential construction, LVL beams are often utilised for header frames above doors and windows, as well as for floor and roof systems. Their capacity to support significant weight makes them indispensable for open-plan living spaces, where structural walls may be minimal.
LVL beams in commercial construction
Commercial buildings frequently employ LVL beams for their large open spaces, aiding in the creation of expansive interiors without compromising structural integrity. Retail spaces, auditoriums, and even warehouses can benefit from the strength and design flexibility LVL beams provide.
Safety considerations when working with LVL beams
While LVL beams offer numerous advantages, it’s important to approach their use with the utmost care. Safety considerations are paramount when handling and installing these structural components.
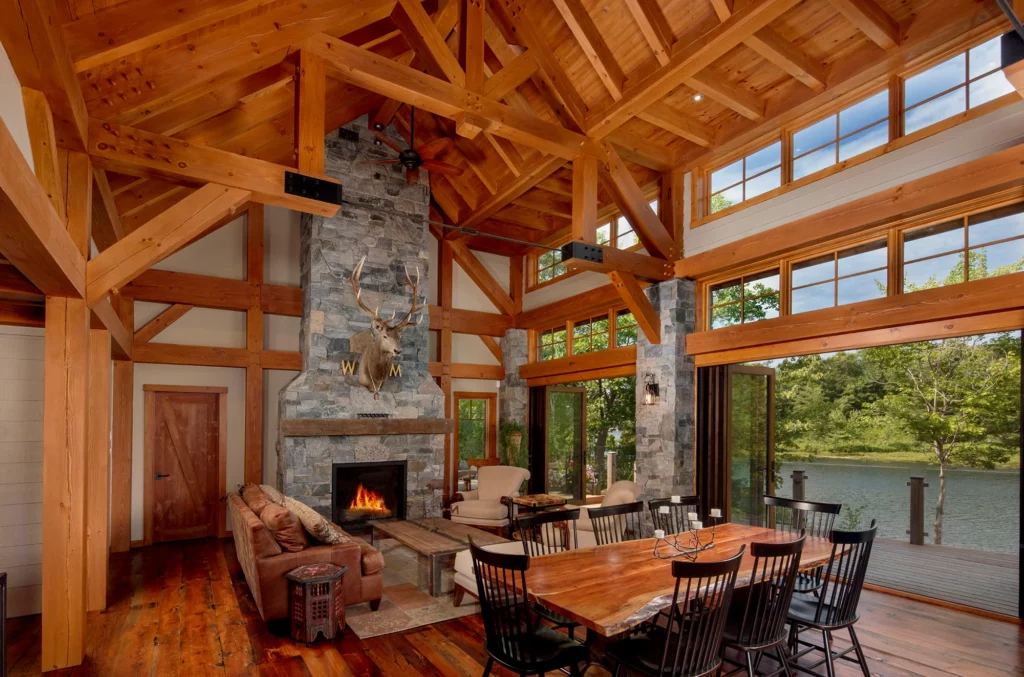
Handling and storage of LVL beams
Proper handling and storage are critical to maintaining the integrity of LVL beams. They should be stored in a dry place, elevated off the ground to prevent moisture absorption. When transporting them, it’s essential to handle with care to prevent any damage that could compromise their performance. To read more about moisture click here.
Installation safety tips for LVL beams
During installation, safety gear such as gloves and hard hats should always be worn. Ensure that beams are installed according to the manufacturer’s specifications, with supports used as necessary to prevent movements. It is also advisable to consult with a structural engineer for larger projects to ensure that load distributions are appropriate.
In conclusion, understanding LVL beams’ fundamental properties, manufacturing processes, benefits, applications, and safety considerations is paramount for any builder. Armed with this knowledge, you can make informed decisions that enhance your construction projects.