Formwork technology plays a vital role in the construction industry, enabling the creation of strong and durable structures. Among the various types of formwork available, Laminated Veneer Lumber (LVL) formwork has gained prominence due to its distinct advantages and innovative design. In this article, we will explore the evolution of LVL formwork technology, its key components, historical background, advancements, and future trends.
Understanding LVL Formwork Technology
Definition and Basic Principles of LVL Formwork
Laminated Veneer Lumber (LVL) formwork is a construction technique that utilizes engineered wood made from thin layers of veneer bonded together with adhesives. LVL formwork offers high strength, durability, and dimensional stability, making it an ideal choice for various construction applications.
The basic principle behind lvl construction is to create temporary molds or frameworks that hold fresh concrete in place during the curing process. This allows the concrete to acquire its desired shape and strength, ensuring the structural integrity of the final building.
But let’s dive deeper into the fascinating world of LVL formwork and explore its key components and their roles in the construction process.
Key Components of LVL Formwork
LVL formwork consists of several key components that work together to provide efficient and effective concrete molding. These components include LVL panels, walers, props, connectors, and accessories.
LVL panels serve as the main structural element and provide the framework for the formwork. These panels are not only lightweight and easy to handle, but they can also be customized to fit specific project requirements. This flexibility allows construction professionals to create intricate and complex concrete structures with ease.
Supporting the LVL panels are walers, which play a crucial role in distributing the load evenly across the formwork system. By evenly distributing the weight of the concrete, walers help maintain the stability and integrity of the formwork, ensuring a smooth and successful construction process.
Props, connectors, and accessories are also vital in maintaining the stability and strength of the formwork. Props provide additional support and prevent the formwork from collapsing under the weight of the concrete. These adjustable props can be easily modified to accommodate different heights and angles, making them indispensable tools for construction professionals.
Connectors, on the other hand, ensure the proper alignment and connection of the formwork components. These connectors act as the glue that holds the formwork together, creating a seamless and secure structure. From simple clamps to more advanced locking systems, connectors play a crucial role in ensuring the overall stability and safety of the formwork system.
Lastly, accessories such as release agents and form ties enhance the ease of use and efficiency of the LVL formwork system. Release agents are applied to the formwork surface to prevent the concrete from sticking, allowing for easy removal once the curing process is complete. Form ties, on the other hand, are used to secure the formwork panels together, ensuring that they remain in place during the pouring and curing of the concrete.
By understanding the key components and principles of LVL formwork, construction professionals can harness the full potential of this innovative technology. With its strength, durability, and versatility, LVL formwork continues to revolutionize the construction industry, enabling the creation of remarkable structures that stand the test of time.
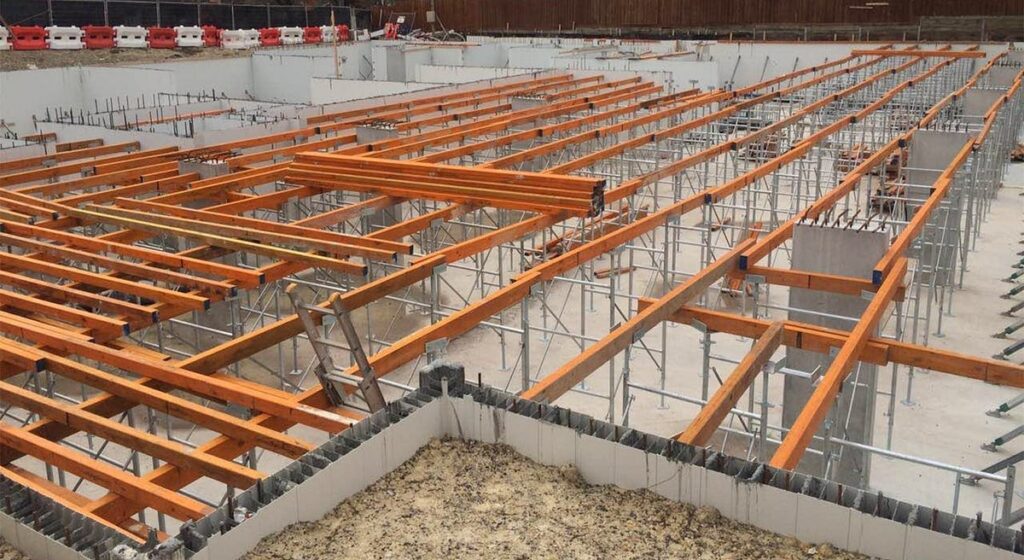
Historical Overview of Formwork Technology
Traditional Formwork Techniques
Before the advent of LVL formwork, traditional formwork techniques such as timber and steel formwork were commonly used in the construction industry. Timber formwork involved using wooden planks and beams to create molds, while steel formwork utilized metal frames and panels.
Although these traditional techniques were effective, they had their limitations. Timber formwork was prone to warping, shrinking, and swelling, leading to difficulties in achieving precise shapes and dimensions. Steel formwork, while more durable, was heavy, expensive, and required skilled labor for installation and dismantling. Learn more about shrinking visit at https://digitalcommons.nyls.edu/nyls_law_review/vol63/iss1/4/.
Despite these challenges, timber formwork held a certain charm due to its natural aesthetic appeal. The warmth and texture of wood added a rustic touch to construction sites, creating a nostalgic ambiance reminiscent of traditional craftsmanship. On the other hand, the sleek and industrial look of steel formwork conveyed a sense of modernity and precision, reflecting the advancements in engineering and technology.
Introduction of LVL Formwork
The introduction of LVL formwork revolutionized the construction industry by providing a lightweight, versatile, and cost-effective alternative to traditional formwork. LVL formwork gained popularity in the late 20th century, with its superior strength-to-weight ratio and dimensional stability. Learn more about cost-effective click here.
LVL formwork allowed for faster assembly, reduced labor costs, and improved efficiency in concrete molding. The flexibility of LVL panels enabled the creation of complex architectural forms, giving architects and designers greater freedom in realizing their creative visions.
Moreover, the environmental benefits of LVL formwork cannot be overlooked. Made from sustainable plantation timber, LVL panels are eco-friendly and contribute to green building practices. This shift towards more sustainable construction methods aligns with the growing global emphasis on environmental conservation and reducing carbon footprints in the built environment.
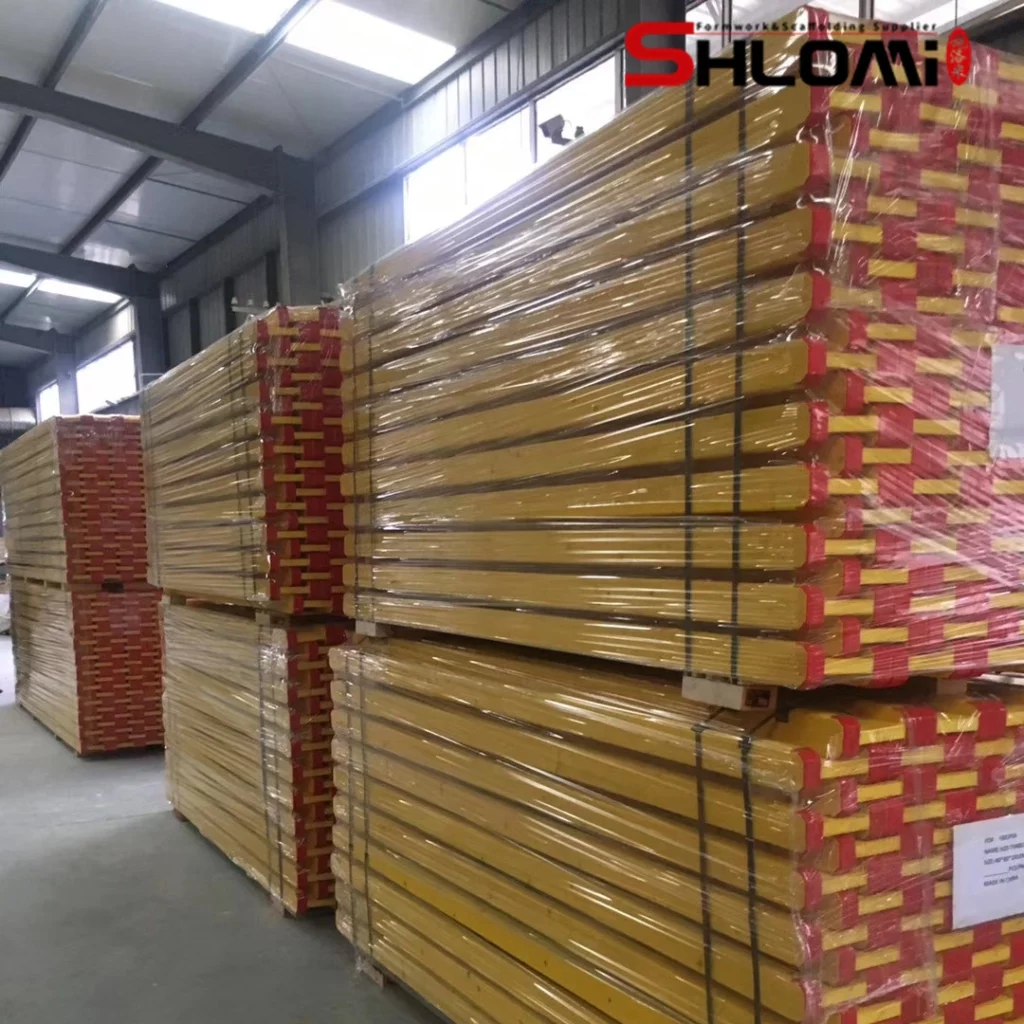
Advancements in LVL Formwork Technology
Technological Innovations in LVL Formwork
Over the years, advancements in LVL formwork technology have further enhanced its performance and usability. Technological innovations, such as the development of high-strength adhesives and advanced manufacturing techniques, have resulted in LVL panels with increased load-bearing capacity and improved durability.
Furthermore, the integration of computer-aided design (CAD) and computer-aided manufacturing (CAM) technologies has allowed for precise customization and optimization of LVL formwork systems. This has led to increased efficiency, reduced material wastage, and enhanced constructability.
One of the key advancements in LVL formwork technology is the incorporation of sustainable practices. Manufacturers are now focusing on using eco-friendly adhesives and sourcing materials from responsibly managed forests. This shift towards sustainability not only benefits the environment but also aligns with the growing demand for green construction practices. Learn more about Maintaining LVL Formwork for Repeated Use: Best Practices visit at https://socialmarketingjournal.com/maintaining-lvl-formwork-for-repeated-use-best-practices/
Impact of Digitalization on LVL Formwork
The digital revolution has had a significant impact on the construction industry, including the field of formwork technology. The emergence of Building Information Modeling (BIM) and construction management software has revolutionized the planning, design, and execution of construction projects.
LVL formwork manufacturers have embraced digitalization by integrating BIM capabilities into their products. This integration enables seamless collaboration, reduces errors, and facilitates better communication among project stakeholders. The use of digital technologies has also opened up opportunities for predictive analytics and machine learning, leading to improved construction processes and cost savings.
Moreover, the adoption of augmented reality (AR) and virtual reality (VR) technologies in LVL formwork design and installation has transformed the way construction teams visualize and interact with formwork systems. These immersive technologies allow for real-time simulations, clash detection, and on-site training, ultimately improving productivity and safety on construction sites.
Benefits of Using LVL Formwork in Construction
Efficiency and Productivity Gains
One of the major benefits of using LVL formwork in construction is the significant increase in efficiency and productivity. The lightweight nature of LVL panels allows for easier handling, transportation, and assembly, reducing labor time and costs. The rapid assembly and dismantling of LVL formwork systems enable faster construction cycles, resulting in overall project time savings.
Additionally, LVL formwork offers excellent dimensional stability, reducing the need for rework or adjustments. This helps to minimize errors and ensures accurate concrete shaping, contributing to enhanced project quality and client satisfaction.
Moreover, the versatility of LVL formwork allows for intricate designs and shapes to be easily achieved, providing architects and engineers with more creative freedom in their construction projects. The smooth surface of LVL panels also results in a high-quality finish on concrete structures, enhancing the aesthetic appeal of the final product.
Environmental and Sustainability Advantages
LVL formwork is considered to be an environmentally friendly alternative to other formwork materials. The production of LVL panels involves less energy consumption and generates fewer greenhouse gas emissions compared to traditional formwork materials.
Furthermore, LVL formwork can be reused multiple times, reducing the amount of waste generated during construction. By promoting the reuse of formwork components, LVL formwork contributes to a more sustainable construction industry by minimizing resource depletion and landfill waste.
In addition, the use of LVL formwork in construction projects can help achieve green building certifications such as LEED (Leadership in Energy and Environmental Design) by reducing the environmental impact of the construction process. This not only benefits the environment but also enhances the reputation of the construction company as a socially responsible and eco-conscious organization.
Future Trends in LVL Formwork Technology
Predicted Technological Developments
The future of LVL formwork technology looks promising, with several predicted advancements on the horizon. Continuous research and development efforts aim to further improve LVL panels’ structural performance, durability, and fire resistance.
Integration with smart sensors and Internet of Things (IoT) technologies could provide real-time monitoring and data analytics capabilities, enabling proactive maintenance and ensuring safe working conditions. The incorporation of automation and robotics in formwork assembly and dismantling processes may also enhance productivity and reduce reliance on manual labor.
One exciting area of research involves the use of nanotechnology in LVL formwork. By incorporating nanomaterials into the manufacturing process, engineers hope to enhance the strength and durability of LVL panels even further. These nanomaterials can improve the resistance of LVL formwork to moisture, mold, and other environmental factors, increasing its lifespan and reducing the need for frequent replacements.
The Role of LVL Formwork in Smart Construction
As the construction industry embraces the concept of smart construction, LVL formwork is expected to play a vital role. LVL panels with embedded sensors could provide valuable data on formwork performance, concrete curing, and structural integrity. This data can be utilized for predictive maintenance, quality control, and optimization of construction processes.
Furthermore, researchers are exploring the possibility of integrating LVL formwork with advanced energy harvesting technologies. By incorporating solar panels or piezoelectric materials into the surface of LVL panels, it may be possible to generate electricity from the vibrations and movements that occur during the construction process. This energy could then be used to power on-site equipment or even feed back into the grid, making construction sites more sustainable and reducing reliance on external power sources.
Additionally, the integration of LVL formwork with other smart technologies, such as prefabrication and modular construction, can lead to increased off-site manufacturing, shorter construction timeframes, and improved project efficiency.
With the rise of 3D printing in the construction industry, researchers are also exploring the feasibility of using LVL materials as a substrate for 3D printed structures. The high strength and dimensional stability of LVL panels make them an ideal candidate for supporting the layers of 3D printed concrete, enabling the construction of complex and customized structures with ease.
In conclusion, the evolution of LVL formwork technology has significantly influenced the construction industry, offering numerous advantages over traditional formwork techniques. With advancements in design, manufacturing processes, and digitalization, LVL formwork provides increased efficiency, productivity gains, environmental benefits, and possibilities for future innovations. As the construction industry moves towards smarter and sustainable practices, LVL formwork continues to be at the forefront of technological advancements, shaping the future of construction.